In today’s competitive marketplace, the role of a Quality Control Specialist has never been more crucial. These professionals are the guardians of product integrity, ensuring that every item meets stringent standards before it reaches consumers. With industries ranging from manufacturing to pharmaceuticals relying heavily on quality assurance, understanding the responsibilities and skills required for this position is essential for both aspiring specialists and employers alike.
This comprehensive guide delves into the multifaceted job description of a Quality Control Specialist, shedding light on the key duties, necessary qualifications, and the impact of their work on overall business success. Whether you’re looking to embark on a career in quality control or seeking to enhance your team’s effectiveness, this article will equip you with valuable insights and practical knowledge. Join us as we explore the vital role of Quality Control Specialists and what it takes to excel in this dynamic field.
Exploring the Role of a Quality Control Specialist
Definition and Scope
A Quality Control Specialist (QCS) plays a crucial role in ensuring that products and services meet specific standards of quality before they reach the consumer. This position is vital across various industries, including manufacturing, pharmaceuticals, food production, and technology. The primary objective of a Quality Control Specialist is to identify defects or inconsistencies in products and processes, thereby safeguarding the company’s reputation and ensuring customer satisfaction.
The scope of a Quality Control Specialist’s work encompasses a wide range of activities, from developing quality standards and procedures to conducting inspections and tests. They are responsible for implementing quality assurance protocols and ensuring compliance with industry regulations. This role requires a keen eye for detail, analytical skills, and a thorough understanding of quality management systems.
Key Responsibilities
The responsibilities of a Quality Control Specialist can vary depending on the industry and the specific organization. However, several core responsibilities are common across most sectors:
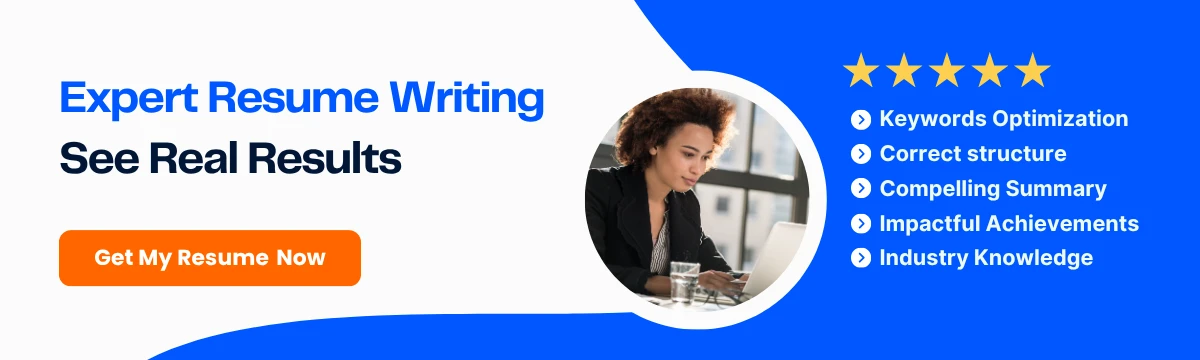
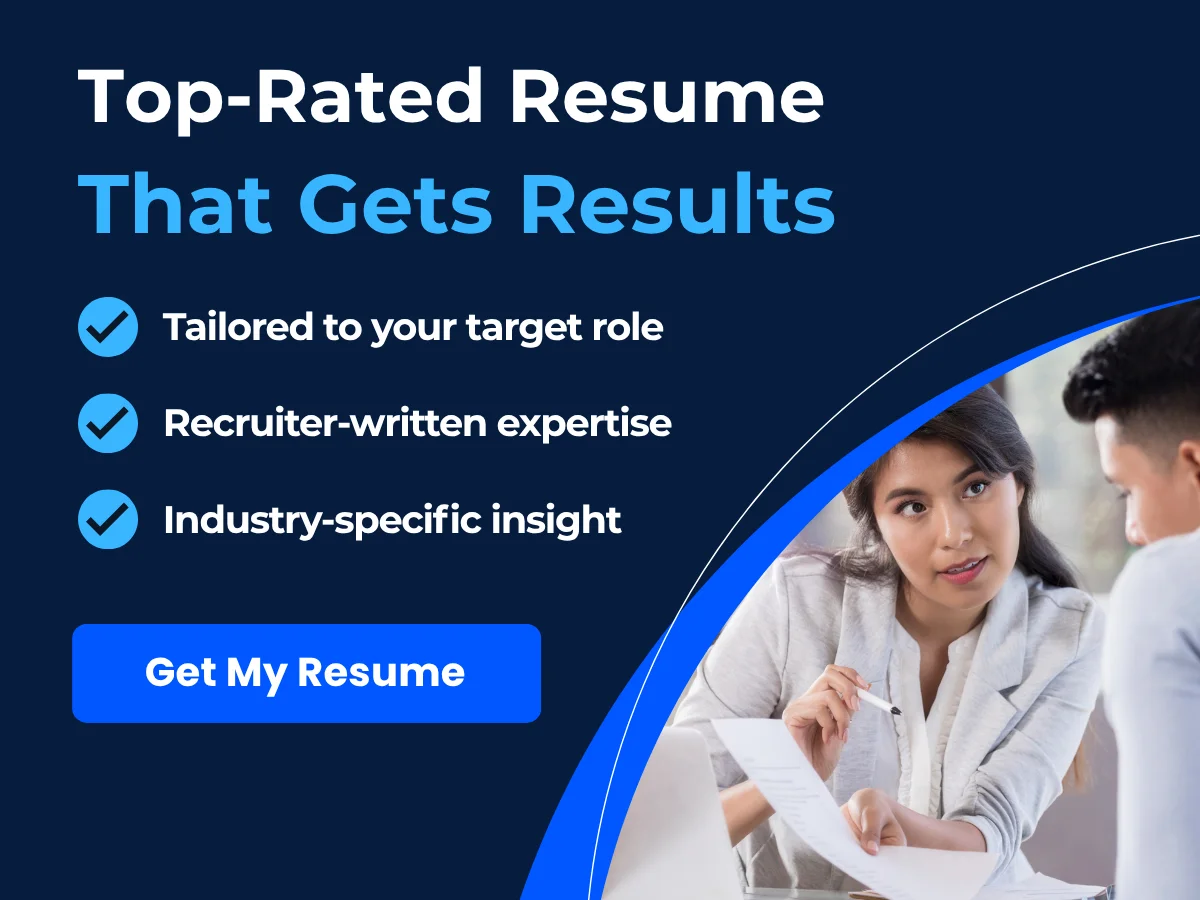
- Developing Quality Standards: QCSs are tasked with creating and maintaining quality standards that align with industry regulations and customer expectations. This involves researching best practices and staying updated on relevant laws and guidelines.
- Conducting Inspections: One of the primary duties of a Quality Control Specialist is to perform regular inspections of products and processes. This may include visual inspections, measurements, and testing to ensure compliance with established standards.
- Data Analysis: Quality Control Specialists collect and analyze data related to product quality. This analysis helps identify trends, potential issues, and areas for improvement. They often use statistical tools and software to interpret data effectively.
- Reporting Findings: After conducting inspections and analyses, QCSs must document their findings and report them to management. This includes creating detailed reports that outline any defects, non-conformities, or areas needing improvement.
- Implementing Corrective Actions: When quality issues are identified, Quality Control Specialists work with relevant teams to develop and implement corrective actions. This may involve revising processes, retraining staff, or adjusting materials used in production.
- Training Staff: Quality Control Specialists often play a role in training employees on quality standards and procedures. They may conduct workshops or create training materials to ensure that all staff members understand their responsibilities regarding quality control.
- Maintaining Documentation: Keeping accurate records is essential in quality control. QCSs are responsible for maintaining documentation related to inspections, tests, and compliance with quality standards. This documentation is crucial for audits and regulatory compliance.
- Collaboration with Other Departments: Quality Control Specialists frequently collaborate with other departments, such as production, engineering, and supply chain management, to ensure that quality standards are integrated throughout the organization.
Daily Tasks and Activities
The daily activities of a Quality Control Specialist can be diverse and dynamic, depending on the specific industry and the organization’s needs. Here’s a closer look at what a typical day might entail:
Morning Routine
Most Quality Control Specialists start their day by reviewing quality reports from the previous day. This includes analyzing data from inspections and tests, identifying any recurring issues, and prioritizing tasks for the day. They may also attend morning meetings with the quality assurance team to discuss ongoing projects, quality metrics, and any immediate concerns that need to be addressed.
Conducting Inspections
After the morning briefing, QCSs often head to the production floor or laboratory to conduct inspections. This may involve:
- Performing visual inspections of products to check for defects.
- Using measuring tools and equipment to ensure products meet specified dimensions and tolerances.
- Conducting tests, such as stress tests or chemical analyses, depending on the product type.
For example, in a manufacturing setting, a Quality Control Specialist might inspect a batch of electronic components to ensure they meet safety and performance standards. In a food production facility, they may test samples for microbial contamination or verify that packaging meets regulatory requirements.
Data Collection and Analysis
After inspections, Quality Control Specialists collect data and begin the analysis process. This involves entering data into quality management software, using statistical methods to identify trends, and generating reports. For instance, if a particular product consistently fails to meet quality standards, the QCS will analyze the data to determine the root cause and recommend corrective actions.
Collaboration and Communication
Throughout the day, Quality Control Specialists communicate with various teams. They may meet with production managers to discuss quality issues, collaborate with engineers to improve product designs, or work with suppliers to ensure that raw materials meet quality standards. Effective communication is essential, as it helps foster a culture of quality within the organization.
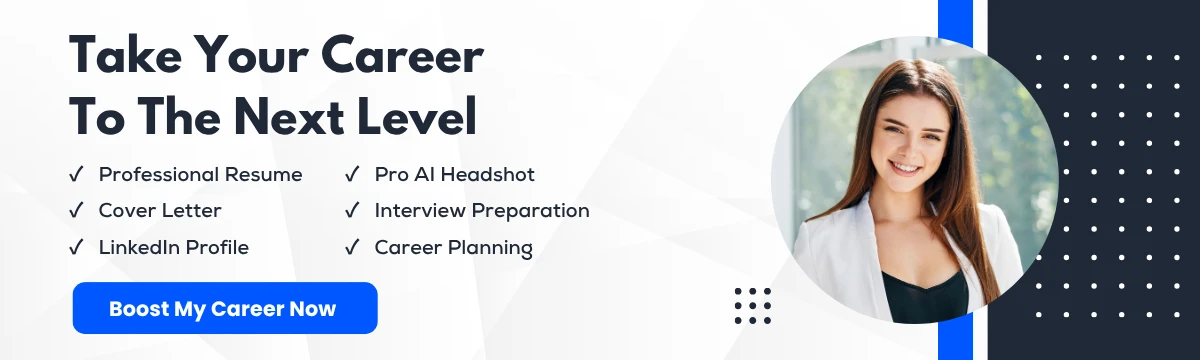
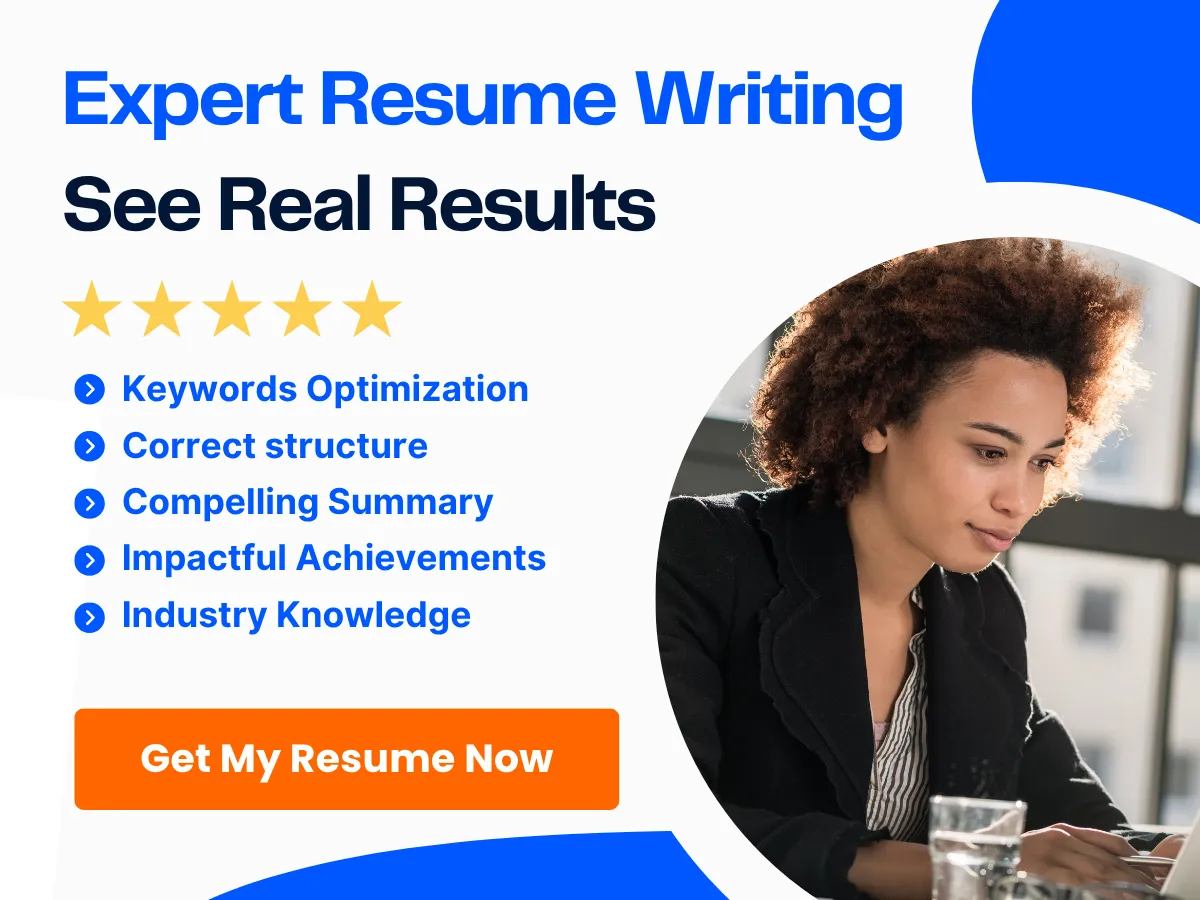
Training and Development
Quality Control Specialists often dedicate part of their day to training staff on quality standards and procedures. This may involve conducting workshops, creating training materials, or providing one-on-one coaching. For example, if a new quality control process is implemented, the QCS will ensure that all relevant employees are trained and understand the new requirements.
Documentation and Reporting
At the end of the day, Quality Control Specialists spend time documenting their findings and preparing reports. This includes updating quality logs, writing inspection reports, and compiling data for management review. Accurate documentation is critical, as it provides a record of compliance and is essential for audits and regulatory inspections.
Continuous Improvement
Quality Control Specialists are also involved in continuous improvement initiatives. They may participate in quality improvement projects, such as Six Sigma or Lean Manufacturing, to enhance processes and reduce waste. This proactive approach not only improves product quality but also contributes to overall operational efficiency.
The role of a Quality Control Specialist is multifaceted and integral to maintaining high standards of quality within an organization. Their daily tasks involve a combination of inspections, data analysis, collaboration, training, and documentation, all aimed at ensuring that products and services meet or exceed customer expectations. As industries continue to evolve, the importance of quality control will only grow, making this a vital career path for those interested in quality assurance and management.
Essential Skills and Qualifications
Quality Control Specialists play a crucial role in ensuring that products meet specific standards of quality, safety, and performance. To excel in this position, candidates must possess a combination of educational qualifications, technical skills, soft skills, and relevant certifications. This section delves into each of these essential components, providing a comprehensive overview of what it takes to succeed as a Quality Control Specialist.
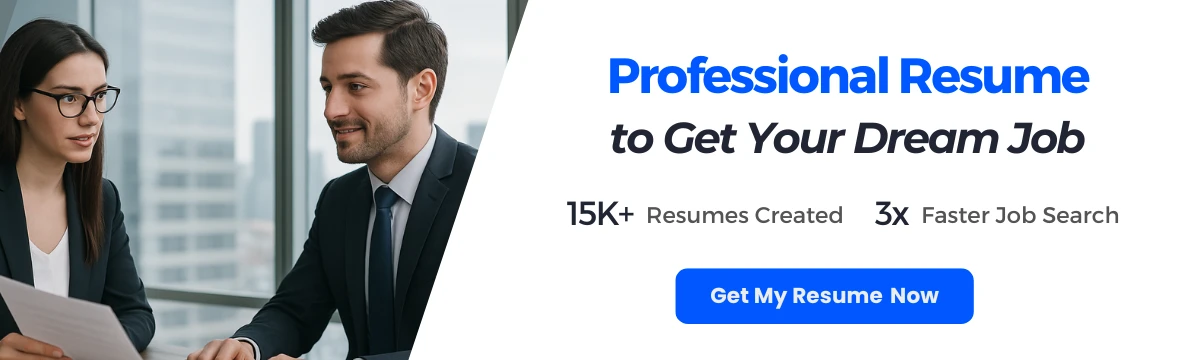
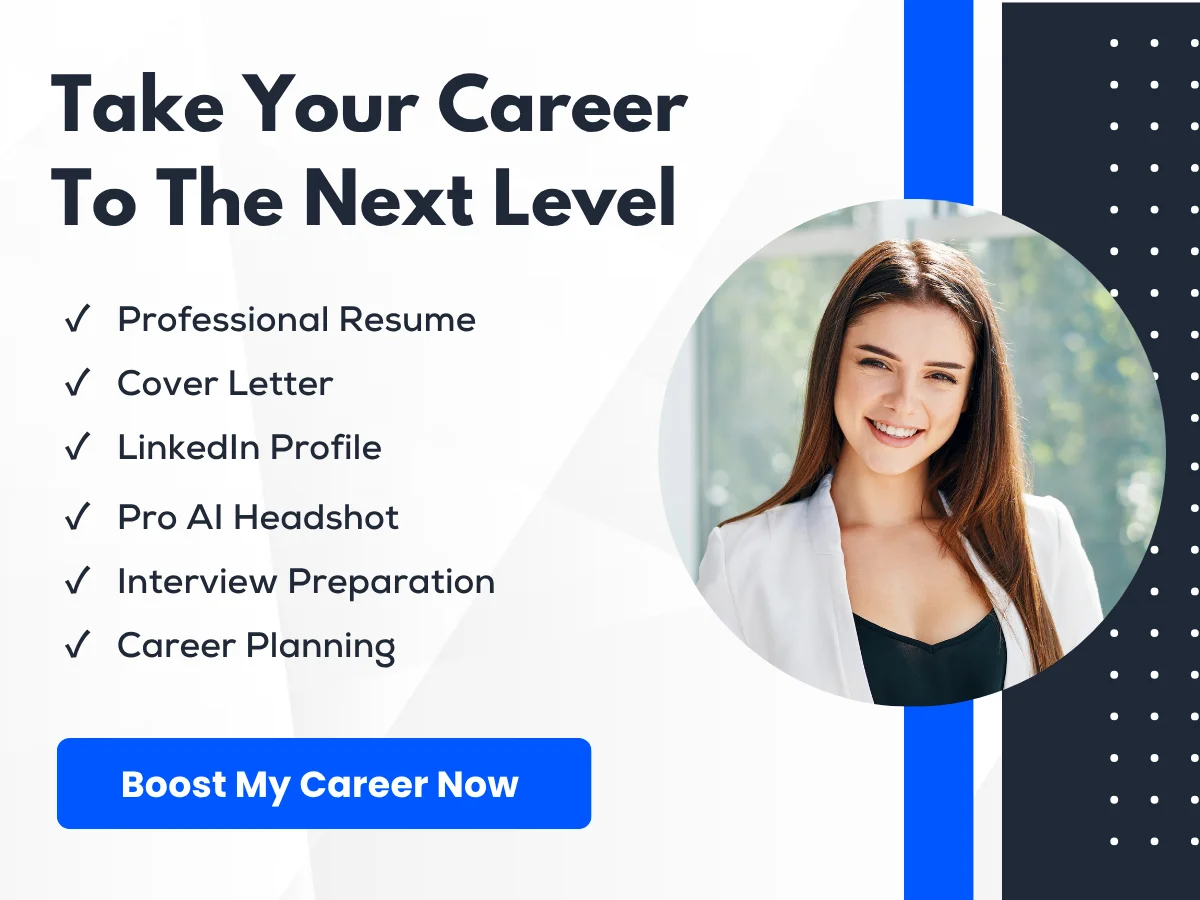
Educational Requirements
Most employers require Quality Control Specialists to have at least a bachelor’s degree in a relevant field. Common areas of study include:
- Quality Assurance: Programs focused on quality management principles, methodologies, and practices.
- Engineering: Degrees in industrial, mechanical, or manufacturing engineering provide a strong technical foundation.
- Biotechnology or Life Sciences: For those working in pharmaceutical or food industries, a background in these fields is often essential.
- Statistics: Understanding statistical methods is crucial for analyzing data and ensuring quality standards.
In addition to formal education, some positions may require specialized training or coursework in quality control methodologies such as Six Sigma, Total Quality Management (TQM), or ISO standards. Continuous education is also encouraged, as it helps professionals stay updated with the latest industry trends and technologies.
Technical Skills
Technical skills are vital for Quality Control Specialists, as they often work with various tools and technologies to assess product quality. Key technical skills include:
- Statistical Analysis: Proficiency in statistical tools and software (e.g., Minitab, SPSS) is essential for analyzing data and identifying trends.
- Quality Control Tools: Familiarity with tools such as control charts, process mapping, and root cause analysis techniques is crucial for effective quality management.
- Inspection Techniques: Knowledge of various inspection methods, including visual inspection, measurement, and testing, is necessary to evaluate product quality.
- Regulatory Standards: Understanding industry-specific regulations (e.g., FDA, ISO 9001) is important for ensuring compliance and maintaining quality standards.
- Software Proficiency: Familiarity with quality management software (e.g., QMS, ERP systems) can streamline processes and improve efficiency.
For example, a Quality Control Specialist in the pharmaceutical industry may need to conduct stability testing and ensure that products meet FDA regulations. This requires a solid understanding of both the technical aspects of the products and the regulatory environment.
Soft Skills
While technical skills are critical, soft skills are equally important for Quality Control Specialists. These skills enable professionals to communicate effectively, work collaboratively, and solve problems efficiently. Key soft skills include:
- Attention to Detail: Quality Control Specialists must be meticulous in their work, as even minor oversights can lead to significant quality issues.
- Analytical Thinking: The ability to analyze data, identify patterns, and draw conclusions is essential for making informed decisions regarding product quality.
- Problem-Solving: Quality Control Specialists often encounter challenges that require innovative solutions. Strong problem-solving skills enable them to address issues promptly and effectively.
- Communication Skills: Clear communication is vital for conveying quality standards, reporting findings, and collaborating with team members and other departments.
- Teamwork: Quality Control Specialists frequently work as part of a team, requiring the ability to collaborate and contribute positively to group efforts.
For instance, a Quality Control Specialist may need to present findings from a quality audit to management. Strong communication skills will help them articulate their observations and recommendations clearly, facilitating informed decision-making.
Certifications and Training Programs
Certifications can enhance a Quality Control Specialist’s credentials and demonstrate their commitment to the field. Several recognized certifications are available, including:

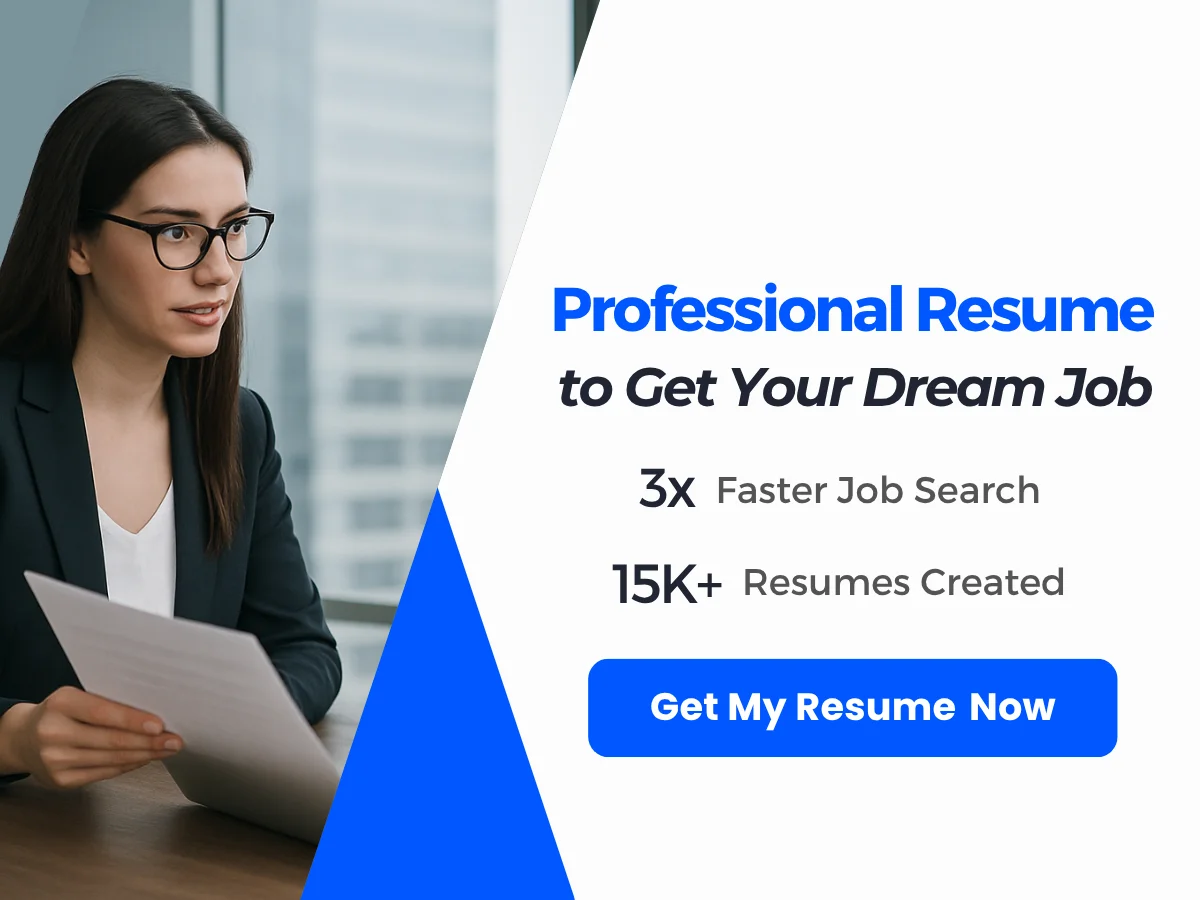
- Certified Quality Auditor (CQA): Offered by the American Society for Quality (ASQ), this certification focuses on auditing quality systems and processes.
- Certified Quality Engineer (CQE): Also provided by ASQ, this certification emphasizes the principles of quality engineering and management.
- Six Sigma Certification: Various organizations offer Six Sigma training and certification, which focuses on process improvement and quality management methodologies.
- ISO 9001 Lead Auditor Certification: This certification demonstrates expertise in auditing quality management systems based on ISO 9001 standards.
In addition to certifications, many organizations offer training programs that cover specific quality control methodologies, tools, and techniques. Participating in workshops, seminars, and online courses can help Quality Control Specialists stay current with industry best practices and enhance their skill sets.
For example, a Quality Control Specialist may choose to pursue Six Sigma Green Belt certification to gain a deeper understanding of process improvement techniques. This knowledge can be applied to streamline operations and enhance product quality within their organization.
The role of a Quality Control Specialist requires a diverse set of skills and qualifications. A solid educational background, technical expertise, strong soft skills, and relevant certifications are all essential components that contribute to success in this field. By continuously developing these skills and staying informed about industry trends, Quality Control Specialists can effectively ensure that products meet the highest standards of quality and safety.
Job Description Template
Sample Job Description
A Quality Control Specialist plays a crucial role in ensuring that products meet specific standards of quality, reliability, and performance. Below is a sample job description that outlines the responsibilities, qualifications, and skills required for this position.
Job Title: Quality Control Specialist Location: [Insert Location] Company: [Insert Company Name] Job Type: [Full-Time/Part-Time/Contract] Job Summary: The Quality Control Specialist is responsible for monitoring and evaluating the quality of products and processes within the organization. This role involves conducting inspections, performing tests, and ensuring compliance with industry standards and regulations. The ideal candidate will have a keen eye for detail, strong analytical skills, and a commitment to maintaining high-quality standards. Key Responsibilities:
- Conduct regular inspections of products and processes to ensure compliance with quality standards.
- Develop and implement quality control procedures and protocols.
- Analyze data from inspections and tests to identify trends and areas for improvement.
- Collaborate with production teams to address quality issues and implement corrective actions.
- Prepare detailed reports on quality metrics and present findings to management.
- Train staff on quality control procedures and best practices.
- Stay updated on industry standards and regulations to ensure compliance.
- Participate in audits and inspections by regulatory agencies.
- Bachelor’s degree in Quality Assurance, Engineering, or a related field.
- Proven experience as a Quality Control Specialist or similar role.
- Strong understanding of quality control methodologies and tools.
- Excellent analytical and problem-solving skills.
- Proficient in using quality control software and tools.
- Strong communication and interpersonal skills.
- Attention to detail and a commitment to quality.
- Certification in Quality Control or Quality Assurance (e.g., Six Sigma, ISO 9001).
- Experience in [specific industry, e.g., manufacturing, pharmaceuticals, food production].
- Competitive salary and performance-based bonuses.
- Health, dental, and vision insurance.
- Retirement savings plan with company match.
- Opportunities for professional development and training.
- Paid time off and flexible work arrangements.
Interested candidates should submit their resume and a cover letter detailing their relevant experience to [Insert Application Email/Link].
Customizing the Template for Different Industries
While the core responsibilities of a Quality Control Specialist remain consistent across various industries, the specific requirements and focus areas can differ significantly. Here are some examples of how to customize the job description template for different sectors:
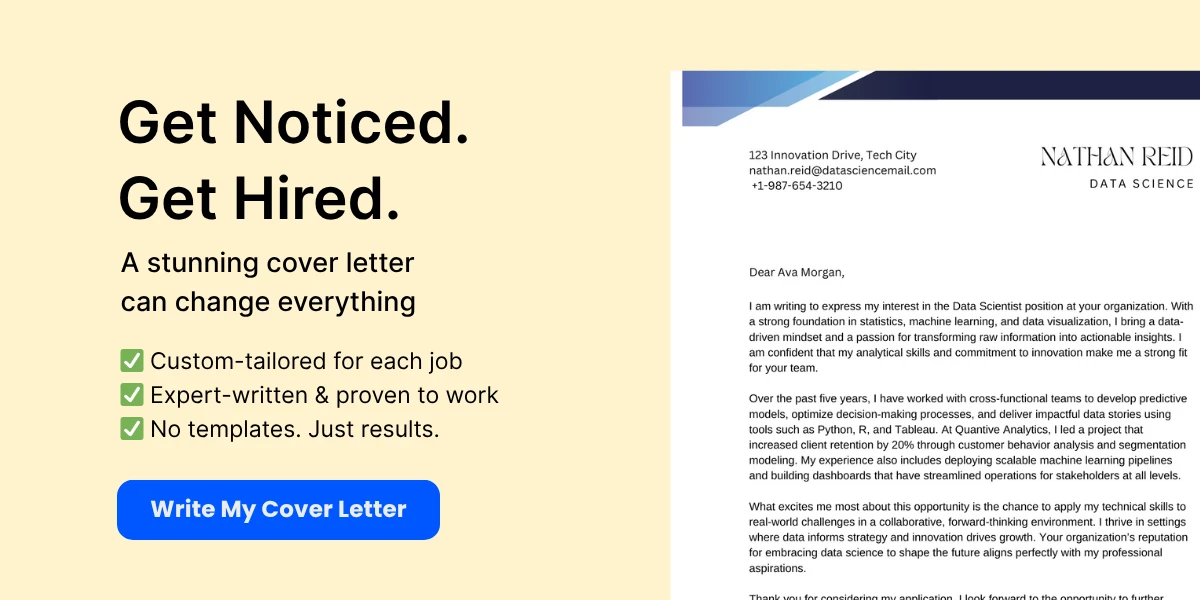
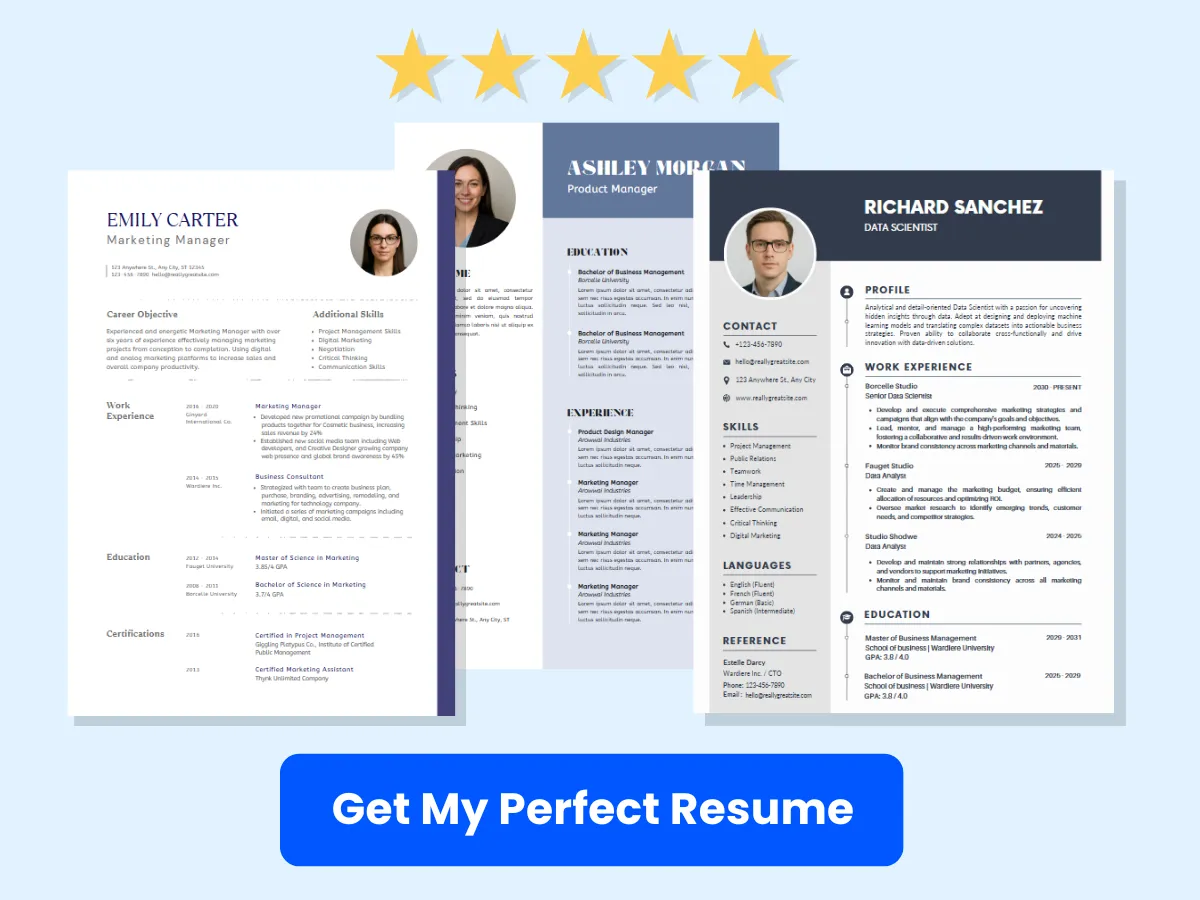
Manufacturing Industry
In the manufacturing sector, the Quality Control Specialist may focus on the following:
- Process Control: Emphasizing the importance of monitoring production processes to minimize defects and ensure efficiency.
- Material Inspection: Highlighting the need for inspecting raw materials and components before they enter the production line.
- Statistical Process Control (SPC): Including knowledge of SPC techniques to analyze production data and improve quality.
Pharmaceutical Industry
For the pharmaceutical industry, the job description should reflect the stringent regulatory requirements:
- Regulatory Compliance: Stressing the importance of adhering to FDA regulations and Good Manufacturing Practices (GMP).
- Documentation: Emphasizing the need for meticulous record-keeping and documentation of quality control processes.
- Testing Protocols: Including specific testing protocols for drug products, such as stability testing and validation processes.
Food Production Industry
In the food production sector, the Quality Control Specialist’s role may include:
- Food Safety Standards: Highlighting knowledge of food safety regulations, such as HACCP (Hazard Analysis Critical Control Point).
- Sanitation Practices: Emphasizing the importance of sanitation and hygiene in food processing environments.
- Product Sampling: Including responsibilities related to sampling and testing food products for quality and safety.
Key Elements to Include
When crafting a job description for a Quality Control Specialist, it is essential to include several key elements to attract the right candidates. Here are the critical components to consider:
Job Title
The job title should be clear and specific. Variations such as “Quality Assurance Specialist,” “Quality Inspector,” or “Quality Control Analyst” can be used depending on the organization’s terminology.
Job Summary
A concise job summary should provide an overview of the role, its importance within the organization, and how it contributes to overall quality assurance efforts.
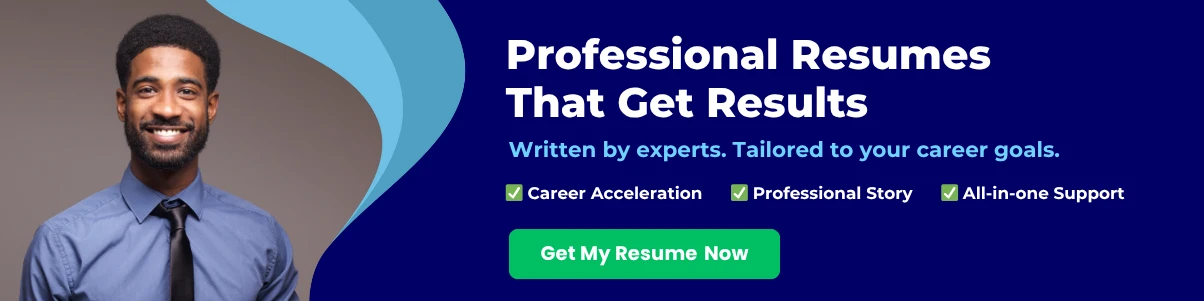
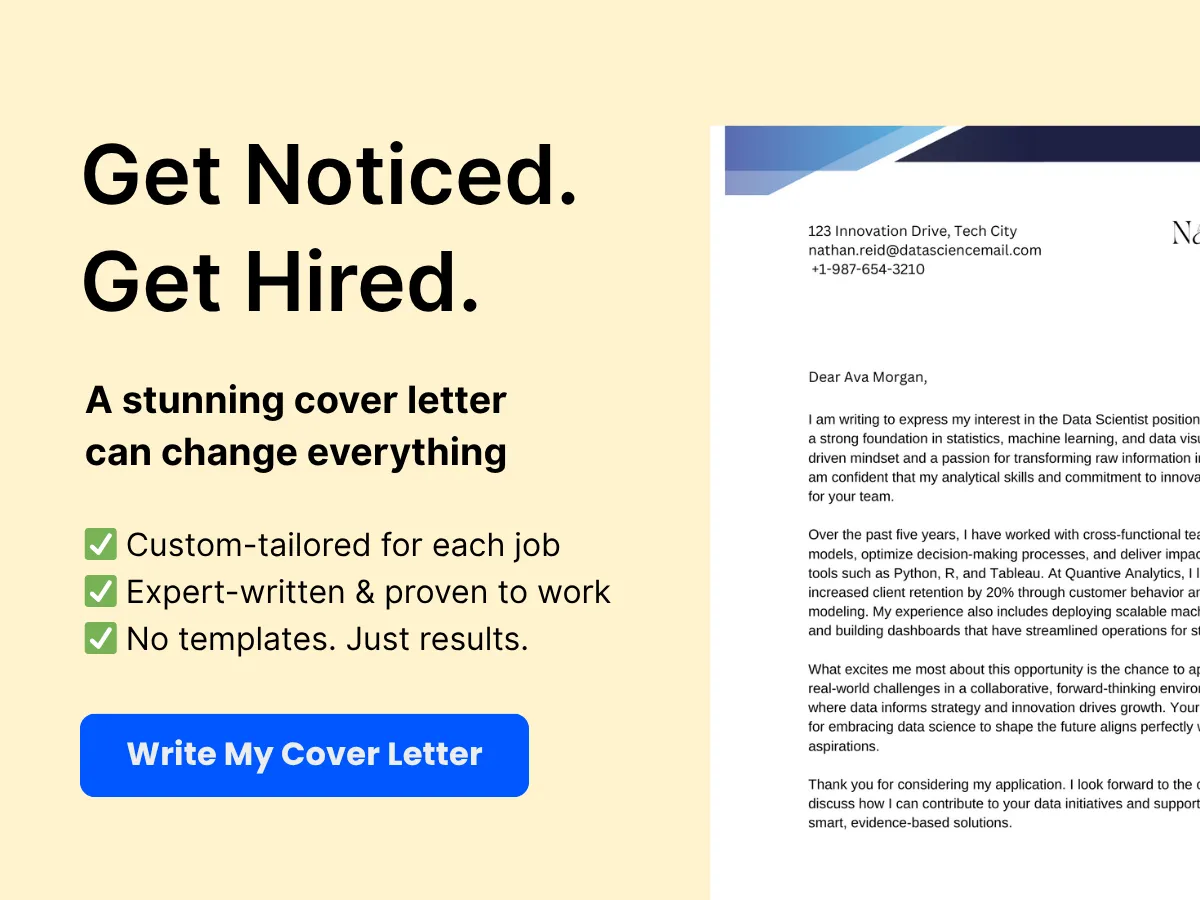
Key Responsibilities
Clearly outline the primary duties and responsibilities associated with the position. Use bullet points for easy readability and ensure that each responsibility is specific and actionable.
Qualifications
List the required and preferred qualifications, including educational background, certifications, and relevant experience. This section helps filter candidates who meet the necessary criteria.
Skills
Highlight the essential skills required for the role, such as analytical thinking, attention to detail, and proficiency in quality control tools and software.
Company Culture and Values
Incorporate a brief description of the company culture and values to attract candidates who align with the organization’s mission and vision. This can help in finding a candidate who not only has the right skills but also fits well within the team.
Application Process
Provide clear instructions on how candidates can apply for the position, including any specific documents required (e.g., resume, cover letter) and the application deadline.
By including these key elements in the job description, organizations can effectively communicate their expectations and attract qualified candidates for the Quality Control Specialist role.
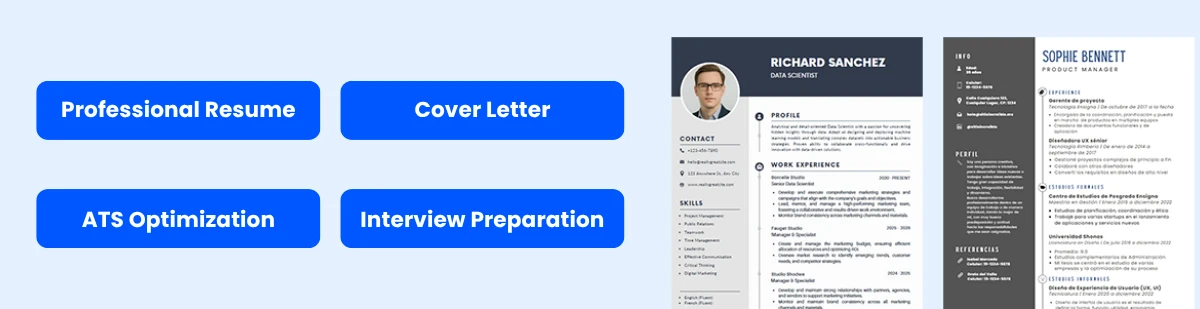
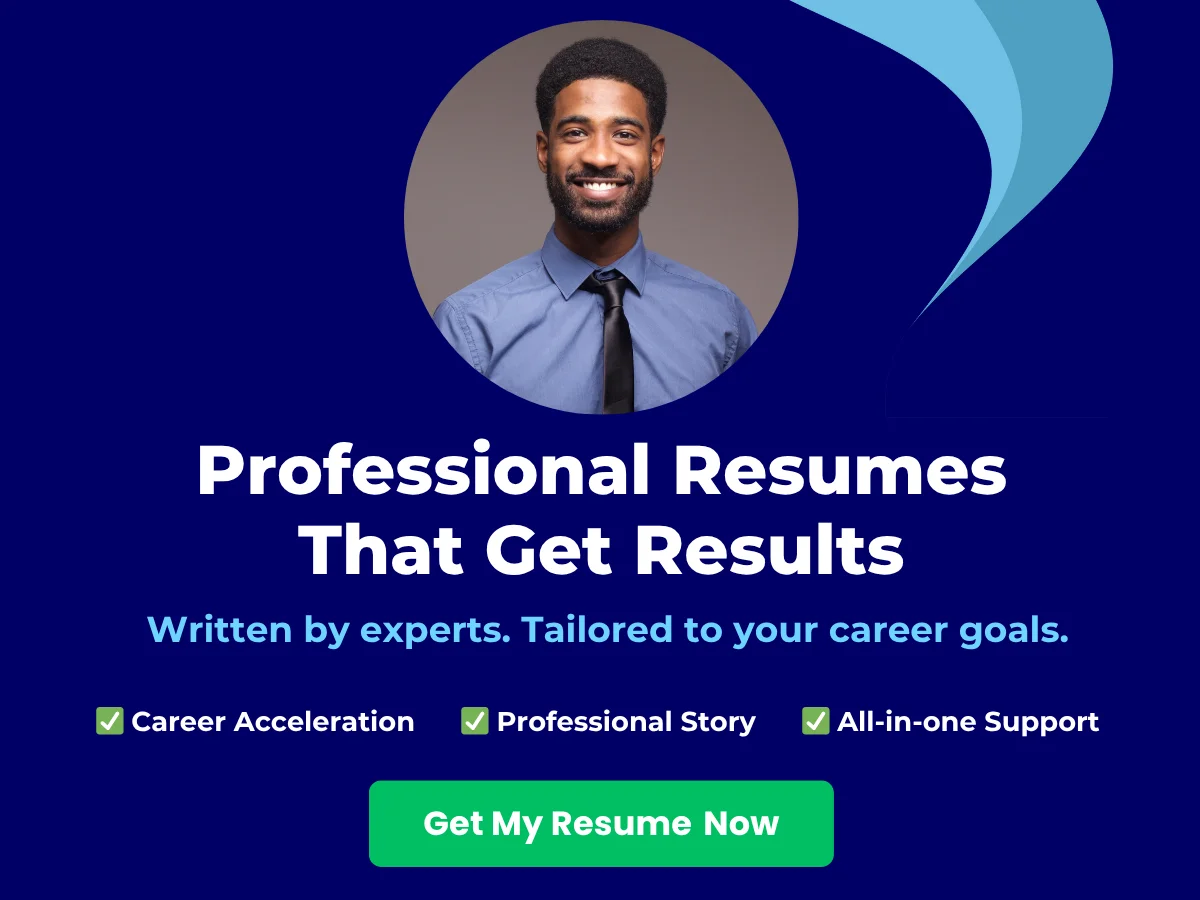
Work Environment and Conditions
Typical Work Settings
Quality Control Specialists (QCS) play a crucial role in ensuring that products meet specific standards of quality before they reach consumers. Their work environments can vary significantly depending on the industry they are in. Here are some common settings where QCS typically operate:
- Manufacturing Facilities: Many Quality Control Specialists work in manufacturing plants, where they inspect products during various stages of production. This environment often includes assembly lines, machinery, and raw materials. Specialists may be involved in both the quality assurance of incoming materials and the final inspection of finished products.
- Laboratories: In industries such as pharmaceuticals, food production, and cosmetics, QCS may work in laboratories where they conduct tests and analyses on samples. These labs are equipped with specialized equipment and adhere to strict safety and regulatory standards.
- Office Settings: Some Quality Control Specialists may work in office environments, particularly in roles that involve data analysis, reporting, and compliance documentation. Here, they may collaborate with other departments, such as production, engineering, and management, to ensure quality standards are met.
- Field Work: In certain industries, such as construction or environmental services, QCS may conduct inspections and assessments on-site. This could involve visiting construction sites, manufacturing plants, or other locations to evaluate compliance with quality standards.
Regardless of the setting, Quality Control Specialists must be adaptable and able to work in various environments, often requiring them to switch between hands-on inspections and analytical tasks.
Physical and Mental Demands
The role of a Quality Control Specialist can be physically and mentally demanding. Understanding these demands is essential for anyone considering a career in this field.
Physical Demands
Quality Control Specialists often engage in tasks that require physical stamina and dexterity. Some of the physical demands include:
- Standing for Long Periods: Many QCS roles require standing for extended periods, especially in manufacturing settings where they monitor production lines.
- Lifting and Carrying: Depending on the industry, QCS may need to lift and carry materials or products, which can weigh anywhere from a few pounds to several hundred pounds.
- Manual Dexterity: Inspecting products often requires fine motor skills, as specialists may need to handle small components or use precision tools for measurements.
- Use of Personal Protective Equipment (PPE): In certain environments, such as laboratories or manufacturing plants, QCS must wear PPE, including gloves, goggles, and masks, to ensure their safety while performing inspections.
Mental Demands
In addition to physical requirements, the mental demands of a Quality Control Specialist can be significant. These include:
- Attention to Detail: QCS must possess a keen eye for detail, as even minor defects can lead to significant issues in product quality. This requires constant focus and vigilance during inspections.
- Problem-Solving Skills: When quality issues arise, QCS must quickly identify the root cause and develop solutions. This often involves critical thinking and analytical skills.
- Data Analysis: Many QCS roles involve analyzing data from inspections and tests. Specialists must be comfortable working with statistical tools and software to interpret results and make informed decisions.
- Communication Skills: Quality Control Specialists often need to communicate findings and recommendations to various stakeholders, including production teams, management, and regulatory bodies. Clear and effective communication is essential.
The combination of physical and mental demands makes the role of a Quality Control Specialist both challenging and rewarding. Those who thrive in this environment often find satisfaction in ensuring that products meet high standards of quality and safety.
Work Schedule and Hours
The work schedule and hours for Quality Control Specialists can vary widely based on the industry, company policies, and specific job requirements. Here are some key considerations regarding their work schedules:
Standard Work Hours
In many manufacturing and production environments, Quality Control Specialists typically work standard business hours, which may range from 8 AM to 5 PM, Monday through Friday. However, this can vary:
- Shift Work: In industries that operate around the clock, such as food processing or pharmaceuticals, QCS may work in shifts, including nights, weekends, and holidays. This is particularly common in facilities that require continuous monitoring of production processes.
- Overtime: During peak production periods or when quality issues arise, Quality Control Specialists may be required to work overtime. This can lead to extended hours and increased workloads, especially in fast-paced environments.
Flexibility and Remote Work
While many Quality Control Specialists work on-site, some roles, particularly those focused on data analysis or compliance documentation, may offer flexibility in terms of remote work. This trend has become more prevalent, especially in the wake of the COVID-19 pandemic, as companies adapt to new work models.
Impact of Industry on Work Schedule
The specific industry can significantly influence the work schedule of a Quality Control Specialist. For example:
- Pharmaceuticals: In this industry, strict regulatory requirements often necessitate rigorous quality checks, which may lead to longer hours and more frequent inspections.
- Food Production: Quality Control Specialists in food production may work irregular hours to ensure compliance with safety standards, especially during peak seasons.
- Manufacturing: In traditional manufacturing settings, QCS may have more predictable schedules, but they must remain flexible to address any quality issues that arise during production.
The work environment and conditions for Quality Control Specialists are diverse and can vary significantly based on the industry and specific job requirements. Understanding these factors is essential for anyone considering a career in quality control, as they can impact job satisfaction, work-life balance, and overall career success.
Career Path and Advancement Opportunities
Embarking on a career as a Quality Control Specialist can be both rewarding and challenging. This profession not only offers a stable job environment but also provides numerous opportunities for growth and specialization. We will explore the various entry-level positions, potential career progression, and specializations within the field of quality control.
Entry-Level Positions
For those just starting their journey in quality control, entry-level positions serve as a crucial stepping stone. These roles typically require a high school diploma or an associate degree, although some employers may prefer candidates with a bachelor’s degree in a related field such as engineering, manufacturing, or quality assurance.
- Quality Control Inspector: This is one of the most common entry-level roles. Quality Control Inspectors are responsible for examining products and materials to ensure they meet specified standards. They conduct tests, document results, and report any defects or issues. This position provides hands-on experience with quality assurance processes and an understanding of industry standards.
- Quality Assurance Technician: Similar to inspectors, QA Technicians focus on testing and evaluating products. They may work closely with production teams to implement quality control measures and ensure compliance with regulations. This role often involves data collection and analysis, making it a great starting point for those interested in the analytical aspects of quality control.
- Quality Control Analyst: This position typically involves more data analysis and reporting than hands-on inspection. Analysts assess quality data, identify trends, and help develop quality improvement strategies. This role is ideal for individuals with strong analytical skills and a keen eye for detail.
These entry-level positions provide foundational knowledge and skills that are essential for advancing in the quality control field. They also offer opportunities to learn about various quality management systems, regulatory requirements, and industry standards.
Career Progression
As Quality Control Specialists gain experience and expertise, they can move up the career ladder into more advanced roles. Career progression in this field can vary based on the industry, company size, and individual performance. Here are some common paths for advancement:
- Senior Quality Control Specialist: After gaining several years of experience, professionals can advance to senior roles. Senior Quality Control Specialists often take on more complex projects, lead teams, and mentor junior staff. They may also be responsible for developing and implementing quality control policies and procedures.
- Quality Control Manager: This managerial position involves overseeing the quality control department and ensuring that all quality standards are met across the organization. Quality Control Managers are responsible for strategic planning, resource allocation, and staff management. They play a critical role in maintaining compliance with industry regulations and improving overall product quality.
- Quality Assurance Director: For those who aspire to higher leadership roles, becoming a Quality Assurance Director is a significant step. This position involves overseeing the entire quality assurance function within an organization, including policy development, compliance, and quality improvement initiatives. Directors often collaborate with other departments to align quality goals with business objectives.
- Quality Consultant: Experienced Quality Control Specialists may choose to work as independent consultants, providing expertise to various organizations. This role allows for flexibility and the opportunity to work on diverse projects across different industries.
Advancement in the quality control field often requires continuous education and professional development. Many professionals pursue certifications such as the Certified Quality Auditor (CQA) or Certified Quality Engineer (CQE) to enhance their credentials and demonstrate their commitment to quality excellence.
Specializations within Quality Control
Quality control is a broad field with numerous specializations that allow professionals to focus on specific areas of interest or expertise. Here are some of the most common specializations within quality control:
- Manufacturing Quality Control: This specialization focuses on ensuring that products are manufactured to meet quality standards. Professionals in this area may work in various industries, including automotive, aerospace, and consumer goods. They are responsible for implementing quality control processes during production and conducting inspections to identify defects.
- Food Quality Control: In the food industry, quality control specialists ensure that products meet safety and quality standards. This specialization involves monitoring production processes, conducting tests for contaminants, and ensuring compliance with food safety regulations. Professionals in this field must have a strong understanding of food science and safety protocols.
- Pharmaceutical Quality Control: Quality control in the pharmaceutical industry is critical for ensuring the safety and efficacy of medications. Specialists in this field conduct rigorous testing and validation of products, monitor manufacturing processes, and ensure compliance with regulatory requirements set by agencies such as the FDA.
- Software Quality Assurance: As technology continues to evolve, the demand for quality control in software development has grown. Software Quality Assurance (QA) specialists focus on testing software applications to identify bugs and ensure functionality. This specialization requires knowledge of programming languages, testing methodologies, and software development life cycles.
- Environmental Quality Control: This specialization involves monitoring and ensuring compliance with environmental regulations. Professionals in this field assess the impact of manufacturing processes on the environment and implement quality control measures to minimize pollution and waste.
Each specialization within quality control offers unique challenges and opportunities. Professionals may choose to focus on one area or develop expertise in multiple specializations, depending on their interests and career goals.
The career path for Quality Control Specialists is diverse and offers numerous opportunities for advancement and specialization. By starting in entry-level positions and gaining experience, professionals can progress to senior roles, management positions, or even consulting. With the right skills and dedication, a career in quality control can lead to a fulfilling and impactful professional journey.
Salary and Compensation
Average Salary Range
The salary of a Quality Control Specialist can vary significantly based on several factors, including geographic location, industry, level of experience, and the specific responsibilities of the role. As of 2023, the average salary for a Quality Control Specialist in the United States typically ranges from $40,000 to $70,000 per year.
Entry-level positions, often requiring minimal experience and basic qualifications, may start at around $35,000 annually. As specialists gain experience and take on more complex tasks, salaries can increase substantially. Mid-level Quality Control Specialists, with several years of experience, can expect to earn between $50,000 and $60,000. Senior-level positions, which may involve supervisory roles or specialized expertise, can command salaries upwards of $70,000 or more.
In addition to base salaries, many Quality Control Specialists may receive bonuses or performance incentives, particularly in industries where quality assurance is critical to business success. For instance, in manufacturing or pharmaceuticals, where product quality directly impacts safety and compliance, performance bonuses can be a significant part of the compensation package.
Factors Influencing Salary
Several factors can influence the salary of a Quality Control Specialist, including:
- Geographic Location: Salaries can vary widely depending on the cost of living in different regions. For example, Quality Control Specialists in metropolitan areas or regions with a high demand for skilled labor, such as California or New York, may earn higher salaries compared to those in rural areas.
- Industry: The industry in which a Quality Control Specialist works can significantly impact salary. Industries such as pharmaceuticals, aerospace, and food production often offer higher salaries due to the stringent quality standards and regulatory requirements they must meet.
- Experience Level: As with many professions, experience plays a crucial role in determining salary. Entry-level positions may offer lower salaries, while those with extensive experience, specialized training, or certifications can command higher pay.
- Education and Certifications: Holding advanced degrees or relevant certifications, such as Six Sigma or ISO 9001, can enhance a Quality Control Specialist’s qualifications and lead to higher salary offers. Employers often value candidates who demonstrate a commitment to professional development.
- Company Size: Larger companies may have more resources to offer competitive salaries and benefits compared to smaller organizations. Additionally, larger firms may have more complex quality control processes, necessitating higher compensation for specialized roles.
Benefits and Perks
In addition to base salaries, Quality Control Specialists often receive a range of benefits and perks that can enhance their overall compensation package. These may include:
- Health Insurance: Most employers offer health insurance plans, which can include medical, dental, and vision coverage. This is a critical benefit that can significantly impact an employee’s overall compensation.
- Retirement Plans: Many companies provide retirement savings plans, such as 401(k) plans, often with employer matching contributions. This benefit helps employees save for their future and can be a substantial part of their overall compensation.
- Paid Time Off: Quality Control Specialists typically receive paid time off (PTO), which may include vacation days, sick leave, and holidays. The amount of PTO can vary based on company policy and the employee’s length of service.
- Professional Development: Employers may offer opportunities for professional development, including training programs, workshops, and conferences. This not only enhances the employee’s skills but can also lead to career advancement and higher salaries.
- Flexible Work Arrangements: Some companies provide flexible work schedules or remote work options, which can improve work-life balance and job satisfaction.
- Performance Bonuses: As mentioned earlier, many Quality Control Specialists may be eligible for performance bonuses based on individual or company performance. These bonuses can provide a significant financial boost.
- Employee Discounts: Depending on the industry, some companies offer employee discounts on products or services, which can add value to the overall compensation package.
The salary and compensation for Quality Control Specialists can be quite competitive, especially for those who invest in their education and professional development. As industries continue to prioritize quality assurance and compliance, the demand for skilled Quality Control Specialists is expected to grow, potentially leading to increased salaries and enhanced benefits in the future.
Challenges and Opportunities in Quality Control
Common Challenges Faced
Quality control specialists play a crucial role in ensuring that products meet specific standards and regulations. However, they often encounter various challenges that can hinder their effectiveness. Understanding these challenges is essential for both current and aspiring quality control professionals.
1. Maintaining Consistency
One of the primary challenges in quality control is maintaining consistency across production processes. Variability in raw materials, equipment performance, and human factors can lead to inconsistencies in product quality. For instance, if a manufacturing plant uses different suppliers for a key component, variations in material quality can affect the final product. Quality control specialists must implement rigorous testing and monitoring protocols to identify and mitigate these inconsistencies.
2. Adapting to Technological Changes
The rapid pace of technological advancement presents both opportunities and challenges for quality control specialists. New technologies, such as automation and artificial intelligence, can enhance quality control processes but also require specialists to continuously update their skills. For example, the integration of machine learning algorithms in quality inspection can improve defect detection rates, but quality control specialists must be trained to interpret and act on the data generated by these systems.
3. Regulatory Compliance
Quality control specialists must navigate a complex landscape of regulations and standards that vary by industry and region. Compliance with these regulations is critical, as failure to do so can result in significant financial penalties and damage to a company’s reputation. For instance, in the pharmaceutical industry, quality control specialists must adhere to stringent guidelines set by the FDA, which requires thorough documentation and validation of processes. Keeping up with changing regulations and ensuring compliance can be a tough task.
4. Resource Limitations
Many quality control departments operate with limited resources, which can impact their ability to perform thorough inspections and testing. Budget constraints may lead to understaffing or insufficient access to advanced testing equipment. Quality control specialists must be adept at prioritizing tasks and finding innovative solutions to maximize the effectiveness of their limited resources. For example, implementing a risk-based approach to quality control can help focus efforts on the most critical areas, ensuring that resources are allocated efficiently.
5. Communication Barriers
Effective communication is vital in quality control, as specialists must collaborate with various departments, including production, engineering, and management. However, communication barriers can arise due to differing priorities and perspectives. Quality control specialists must develop strong interpersonal skills to bridge these gaps and advocate for quality initiatives. Regular meetings, cross-departmental training, and clear documentation can help facilitate better communication and collaboration.
Opportunities for Growth and Development
Despite the challenges, the field of quality control offers numerous opportunities for growth and development. Quality control specialists can enhance their careers by pursuing further education, certifications, and specialized training.
1. Professional Certifications
Obtaining professional certifications can significantly enhance a quality control specialist’s credentials and career prospects. Certifications such as the Certified Quality Engineer (CQE) or Certified Quality Auditor (CQA) from the American Society for Quality (ASQ) demonstrate a commitment to quality and a deep understanding of quality management principles. These certifications can open doors to advanced positions and increase earning potential.
2. Continuous Education
Quality control specialists should engage in continuous education to stay current with industry trends and best practices. This can include attending workshops, webinars, and conferences focused on quality management. Many universities and professional organizations offer courses in quality control methodologies, statistical process control, and Six Sigma, which can provide valuable knowledge and skills applicable to their roles.
3. Cross-Functional Roles
Quality control specialists have the opportunity to transition into cross-functional roles within their organizations. By gaining experience in related areas such as production management, supply chain management, or regulatory affairs, they can broaden their skill set and increase their value to the company. This versatility can lead to leadership positions and greater responsibilities.
4. Leadership Development
As organizations increasingly recognize the importance of quality, there is a growing demand for quality control specialists to take on leadership roles. Developing leadership skills can position quality control specialists for management positions, where they can influence quality initiatives at a strategic level. Participating in leadership training programs and seeking mentorship from experienced leaders can help specialists cultivate these skills.
5. Networking Opportunities
Networking is a powerful tool for career advancement in quality control. Joining professional organizations, such as ASQ or the International Register of Certificated Auditors (IRCA), can provide access to a network of professionals in the field. Networking can lead to job opportunities, collaborations, and valuable insights into industry trends and challenges.
Future Trends in Quality Control
The field of quality control is evolving rapidly, driven by technological advancements and changing consumer expectations. Quality control specialists must stay informed about these trends to remain competitive and effective in their roles.
1. Increased Automation
Automation is transforming quality control processes, allowing for more efficient and accurate inspections. Automated inspection systems, such as vision systems and robotic process automation, can quickly identify defects and reduce human error. Quality control specialists will need to adapt to these technologies, learning how to integrate them into existing processes and interpret the data they generate.
2. Data Analytics and Big Data
The rise of big data and advanced analytics is reshaping quality control. Quality control specialists can leverage data analytics to identify trends, predict potential quality issues, and make data-driven decisions. For example, using statistical process control (SPC) techniques, specialists can analyze production data in real-time to detect anomalies and implement corrective actions before defects occur. This proactive approach can significantly enhance product quality and reduce waste.
3. Emphasis on Sustainability
As consumers become more environmentally conscious, there is a growing emphasis on sustainability in quality control. Quality control specialists will need to consider the environmental impact of production processes and materials. Implementing sustainable practices, such as reducing waste and optimizing resource use, will become increasingly important. Specialists may also be involved in developing quality standards for sustainable products, ensuring that they meet both quality and environmental criteria.
4. Remote Quality Control
The COVID-19 pandemic has accelerated the trend toward remote work, and quality control is no exception. Remote quality control practices, such as virtual inspections and remote monitoring, are becoming more common. Quality control specialists will need to adapt to these new methods, utilizing technology to conduct inspections and audits from a distance. This shift may also require new skills in digital communication and remote collaboration.
5. Focus on Customer Experience
Quality control is increasingly linked to customer experience. Quality control specialists must understand customer expectations and ensure that products not only meet technical specifications but also deliver a positive user experience. This may involve gathering customer feedback, analyzing product performance in real-world conditions, and collaborating with product development teams to enhance product design. By prioritizing customer satisfaction, quality control specialists can contribute to building brand loyalty and trust.
How to Become a Quality Control Specialist
Step-by-Step Guide
Becoming a Quality Control Specialist involves a combination of education, experience, and skill development. Here’s a step-by-step guide to help you navigate the path to this rewarding career.
-
Research the Role
Before embarking on your journey, it’s essential to understand what a Quality Control Specialist does. This role typically involves monitoring and evaluating the quality of products and services, ensuring they meet established standards and regulations. Familiarize yourself with the specific responsibilities, tools, and methodologies used in quality control.
-
Obtain Relevant Education
Most Quality Control Specialist positions require at least a bachelor’s degree in a related field such as quality assurance, engineering, manufacturing, or a science discipline. Some employers may prefer candidates with advanced degrees or certifications in quality management.
-
Gain Practical Experience
Experience is crucial in this field. Seek internships or entry-level positions in quality control or related areas. This hands-on experience will help you understand the practical applications of quality control principles and tools.
-
Develop Key Skills
Quality Control Specialists need a diverse skill set, including:
- Analytical Skills: Ability to analyze data and identify trends.
- Attention to Detail: Precision is critical in quality control.
- Problem-Solving Skills: Ability to identify issues and develop solutions.
- Communication Skills: Effectively communicate findings and recommendations to team members and management.
- Technical Skills: Familiarity with quality control tools and software.
-
Consider Certification
While not always required, obtaining certification can enhance your qualifications. Organizations such as the American Society for Quality (ASQ) offer certifications like the Certified Quality Improvement Associate (CQIA) and Certified Quality Auditor (CQA). These credentials can demonstrate your commitment to the field and your expertise in quality control practices.
-
Network and Seek Mentorship
Networking is vital in any career. Attend industry conferences, join professional organizations, and connect with experienced Quality Control Specialists. A mentor can provide valuable insights and guidance as you navigate your career path.
-
Apply for Positions
Once you have the necessary education and experience, start applying for Quality Control Specialist positions. Tailor your resume and cover letter to highlight your relevant skills and experiences. Be prepared for interviews by practicing common questions related to quality control and demonstrating your knowledge of industry standards.
Educational Pathways
The educational requirements for a Quality Control Specialist can vary depending on the industry and specific job responsibilities. Here’s a breakdown of common educational pathways:
Bachelor’s Degree
A bachelor’s degree is typically the minimum requirement for most Quality Control Specialist positions. Relevant fields of study include:
- Quality Assurance: Programs focused on quality management principles, methodologies, and tools.
- Engineering: Degrees in industrial, mechanical, or manufacturing engineering provide a strong foundation in process optimization and quality control techniques.
- Manufacturing: Programs that cover production processes, materials science, and quality management.
- Science Disciplines: Degrees in chemistry, biology, or other sciences can be beneficial, especially in industries like pharmaceuticals or food production.
Advanced Degrees
While not always necessary, pursuing a master’s degree in quality management or a related field can enhance your career prospects and open doors to higher-level positions. Advanced education often covers more complex quality control concepts, statistical methods, and leadership skills.
Certifications
In addition to formal education, certifications can bolster your qualifications. Some notable certifications include:
- Certified Quality Engineer (CQE): Offered by ASQ, this certification focuses on quality engineering principles and practices.
- Certified Quality Auditor (CQA): This certification demonstrates your ability to assess quality systems and processes.
- Six Sigma Certification: Six Sigma methodologies focus on process improvement and quality management, making this certification valuable in many industries.
Gaining Relevant Experience
Experience is a critical component of becoming a successful Quality Control Specialist. Here are some effective ways to gain relevant experience:
Internships
Internships provide an excellent opportunity to gain hands-on experience in quality control. Look for internships in manufacturing, pharmaceuticals, food production, or any industry that emphasizes quality assurance. During your internship, focus on learning about quality control processes, tools, and methodologies.
Entry-Level Positions
Consider applying for entry-level positions such as Quality Control Technician or Quality Assurance Assistant. These roles often involve supporting quality control processes, conducting inspections, and assisting in data collection and analysis. This experience will help you build a solid foundation in quality control practices.
On-the-Job Training
Many companies offer on-the-job training for new hires. Take advantage of this training to learn about the specific quality control processes and standards used in your organization. Ask questions, seek feedback, and actively participate in quality improvement initiatives.
Professional Development
Continuously seek opportunities for professional development. Attend workshops, webinars, and training sessions related to quality control. Staying updated on industry trends and best practices will enhance your skills and make you a more competitive candidate.
Networking
Networking with professionals in the quality control field can lead to valuable opportunities. Join industry associations, attend conferences, and participate in online forums. Engaging with others in the field can provide insights into job openings, industry standards, and emerging trends.
By following these steps and focusing on education, experience, and skill development, you can successfully navigate your path to becoming a Quality Control Specialist. This role not only offers a chance to ensure product quality but also plays a vital part in enhancing customer satisfaction and driving business success.
Interview Preparation
Common Interview Questions
Preparing for an interview as a Quality Control Specialist requires a solid understanding of both the technical aspects of the role and the soft skills necessary for success. Below are some common interview questions you might encounter, along with insights into what interviewers are looking for in your responses.
1. Can you describe your experience with quality control processes?
This question aims to gauge your familiarity with quality control methodologies. Be prepared to discuss specific processes you have implemented or improved in previous roles. Mention any relevant frameworks, such as Six Sigma, ISO standards, or Total Quality Management (TQM), and provide examples of how you applied these methodologies to enhance product quality.
2. How do you handle discrepancies in product quality?
Interviewers want to assess your problem-solving skills and your ability to remain calm under pressure. Discuss a specific instance where you identified a quality issue, the steps you took to investigate the problem, and how you communicated the findings to your team. Highlight your analytical skills and your ability to implement corrective actions.
3. What tools and software are you proficient in for quality control?
Quality Control Specialists often use various tools and software to monitor and analyze quality metrics. Be prepared to discuss your experience with statistical analysis software (like Minitab), quality management systems (like SAP or Oracle), and any other relevant tools. Mention how these tools have helped you in your previous roles.
4. How do you prioritize tasks when managing multiple quality control projects?
This question assesses your organizational skills and ability to manage time effectively. Discuss your approach to prioritization, such as using project management tools, setting deadlines, and communicating with team members. Provide examples of how you have successfully managed competing priorities in the past.
5. Can you give an example of a time you improved a quality control process?
Interviewers are looking for evidence of your initiative and ability to drive change. Share a specific example where you identified a gap in the quality control process, the steps you took to address it, and the positive outcomes that resulted. Use metrics to quantify your success, such as reduced defects or improved customer satisfaction.
Tips for a Successful Interview
To stand out in your interview for a Quality Control Specialist position, consider the following tips:
1. Research the Company
Before the interview, take the time to research the company’s products, services, and quality standards. Understanding the company’s mission and values will help you tailor your responses to align with their goals. Additionally, familiarize yourself with any recent news or developments related to the company, as this can provide valuable context for your discussion.
2. Prepare Your Own Questions
At the end of the interview, you will likely have the opportunity to ask questions. Prepare thoughtful questions that demonstrate your interest in the role and the company. For example, you might ask about the company’s approach to continuous improvement or how the quality control team collaborates with other departments.
3. Practice Behavioral Interview Techniques
Many interviewers use behavioral interview techniques to assess how you have handled situations in the past. Use the STAR method (Situation, Task, Action, Result) to structure your responses. This approach helps you provide clear and concise answers that highlight your skills and experiences effectively.
4. Dress Professionally
First impressions matter, so dress appropriately for the interview. A professional appearance conveys that you take the opportunity seriously and respect the company’s culture. When in doubt, opt for business formal attire.
5. Follow Up After the Interview
After the interview, send a thank-you email to express your appreciation for the opportunity to interview. This is also a chance to reiterate your interest in the position and briefly mention any key points you may want to emphasize again. A thoughtful follow-up can leave a lasting impression on the interviewer.
What Employers Look For
When interviewing candidates for a Quality Control Specialist position, employers typically seek a combination of technical skills, experience, and personal attributes. Here are some key qualities that employers often prioritize:
1. Technical Proficiency
Employers look for candidates with a strong understanding of quality control principles and methodologies. Familiarity with industry standards, regulatory requirements, and quality management systems is crucial. Demonstrating your ability to use statistical tools and software for data analysis is also highly valued.
2. Attention to Detail
Quality Control Specialists must have a keen eye for detail. Employers want to see that you can identify even the smallest discrepancies in product quality. Highlight experiences where your attention to detail made a significant impact on quality outcomes.
3. Problem-Solving Skills
Employers seek candidates who can think critically and solve problems effectively. Your ability to analyze data, identify root causes of quality issues, and implement corrective actions is essential. Provide examples of how you have successfully navigated challenges in previous roles.
4. Communication Skills
Quality Control Specialists often work with cross-functional teams, so strong communication skills are vital. Employers look for candidates who can clearly articulate quality standards, provide feedback, and collaborate with others. Discuss instances where you effectively communicated quality issues and worked with teams to resolve them.
5. Adaptability
The manufacturing and production environments can be dynamic, and quality control processes may need to evolve. Employers value candidates who can adapt to changing circumstances and remain flexible in their approach. Share examples of how you have successfully adapted to new processes or technologies in your previous roles.
6. Commitment to Continuous Improvement
Employers appreciate candidates who are dedicated to continuous improvement and staying current with industry trends. Discuss any professional development activities you have engaged in, such as certifications, workshops, or conferences, that demonstrate your commitment to enhancing your skills and knowledge in quality control.
By preparing for these common interview questions, following the tips for a successful interview, and understanding what employers are looking for, you can position yourself as a strong candidate for a Quality Control Specialist role. Remember, the interview is not just an opportunity for the employer to assess your fit for the position; it’s also your chance to evaluate whether the company aligns with your career goals and values.
Tools and Technologies Used by Quality Control Specialists
Quality Control (QC) Specialists play a crucial role in ensuring that products meet specific standards of quality and safety. To effectively carry out their responsibilities, they rely on a variety of tools and technologies. This section delves into the essential software, equipment, and emerging technologies that QC specialists utilize in their daily operations.
Software and Applications
In the modern landscape of quality control, software applications have become indispensable. These tools help QC specialists streamline processes, manage data, and enhance communication across teams. Here are some of the most commonly used software and applications:
- Statistical Process Control (SPC) Software: SPC software is vital for monitoring and controlling manufacturing processes. It uses statistical methods to analyze data and identify variations that may indicate potential quality issues. Popular SPC software includes Minitab, JMP, and InfinityQS.
- Quality Management Systems (QMS): A QMS is a comprehensive framework that helps organizations manage quality across all operations. It includes documentation, process management, and compliance tracking. Notable QMS solutions are ISO 9001-compliant systems like MasterControl, ETQ, and Greenlight Guru.
- Document Control Software: QC specialists often need to manage a plethora of documents, including standard operating procedures (SOPs), inspection reports, and compliance records. Document control software like DocuWare and SharePoint helps in organizing, storing, and retrieving these documents efficiently.
- Data Analysis Tools: Tools such as Microsoft Excel, R, and Python libraries (like Pandas and NumPy) are frequently used for data analysis. QC specialists utilize these tools to perform complex calculations, create visualizations, and derive insights from quality data.
- Project Management Software: To coordinate quality control projects and ensure timely completion, QC specialists often use project management tools like Trello, Asana, or Microsoft Project. These platforms help in tracking progress, assigning tasks, and managing deadlines.
Equipment and Instruments
In addition to software, QC specialists rely on various physical instruments and equipment to conduct inspections and tests. The choice of equipment often depends on the industry and the specific quality standards that need to be met. Here are some essential tools:
- Calipers and Micrometers: These precision measuring tools are used to measure dimensions, thickness, and diameters of components. They are crucial in industries like manufacturing and engineering, where tolerances are critical.
- Hardness Testers: Hardness testers, such as Rockwell and Brinell testers, are used to determine the hardness of materials. This is particularly important in metalworking and materials science, where hardness can affect performance and durability.
- Surface Roughness Testers: These instruments measure the texture of a surface, which can impact the performance and aesthetic quality of a product. Surface roughness testers are commonly used in machining and manufacturing processes.
- Visual Inspection Tools: Tools such as magnifying glasses, borescopes, and endoscopes are used for visual inspections. These tools help QC specialists identify defects that may not be visible to the naked eye.
- Environmental Testing Equipment: In industries like pharmaceuticals and food production, maintaining specific environmental conditions is crucial. Equipment such as temperature and humidity loggers, air quality monitors, and cleanroom validation tools are essential for ensuring compliance with quality standards.
Emerging Technologies in Quality Control
The field of quality control is continuously evolving, with new technologies emerging to enhance efficiency and accuracy. Here are some of the most promising trends and technologies that are shaping the future of quality control:
- Artificial Intelligence (AI) and Machine Learning: AI and machine learning algorithms are increasingly being integrated into quality control processes. These technologies can analyze vast amounts of data to identify patterns and predict potential quality issues before they occur. For example, AI can be used to monitor production lines in real-time, flagging anomalies that may indicate defects.
- Internet of Things (IoT): IoT devices are revolutionizing quality control by enabling real-time monitoring of equipment and processes. Sensors can collect data on various parameters, such as temperature, pressure, and humidity, and transmit this information to QC specialists for analysis. This allows for proactive quality management and quicker response times to potential issues.
- Blockchain Technology: Blockchain offers a secure and transparent way to track the quality of products throughout the supply chain. By recording every transaction and inspection on a decentralized ledger, companies can ensure traceability and accountability, which is particularly important in industries like food and pharmaceuticals.
- Robotics and Automation: Automation is becoming increasingly prevalent in quality control processes. Robotic systems can perform repetitive inspection tasks with high precision and speed, reducing the likelihood of human error. Automated inspection systems, such as vision systems, can quickly analyze products for defects and ensure compliance with quality standards.
- Augmented Reality (AR) and Virtual Reality (VR): AR and VR technologies are being explored for training and inspection purposes. For instance, AR can provide QC specialists with real-time data overlays during inspections, enhancing their ability to identify defects. VR can be used for immersive training experiences, allowing new employees to practice quality control procedures in a simulated environment.
As the landscape of quality control continues to evolve, staying updated on the latest tools and technologies is essential for QC specialists. By leveraging these advancements, they can enhance their effectiveness, improve product quality, and contribute to the overall success of their organizations.
Professional Associations and Networking
In the field of quality control, professional associations and networking play a crucial role in career development, knowledge sharing, and staying updated with industry trends. These organizations provide a platform for quality control specialists to connect, learn, and grow within their profession. This section delves into key organizations and societies, the benefits of membership, and the networking opportunities available to quality control professionals.
Key Organizations and Societies
Several prominent organizations and societies focus on quality control and assurance. These entities not only promote best practices but also provide resources, training, and certification programs that can enhance a quality control specialist’s career. Here are some of the most notable organizations:
- American Society for Quality (ASQ): ASQ is one of the largest and most recognized organizations dedicated to quality professionals. It offers a wealth of resources, including certifications, training programs, and a vast library of quality-related publications. ASQ also hosts conferences and events that allow members to network and share knowledge.
- International Organization for Standardization (ISO): While not a membership organization in the traditional sense, ISO develops and publishes international standards, including those related to quality management systems (e.g., ISO 9001). Quality control specialists often engage with ISO standards to ensure compliance and improve processes within their organizations.
- Quality Assurance Institute (QAI): QAI focuses on quality assurance and offers various certifications and training programs. It aims to advance the profession of quality assurance and provides resources for professionals looking to enhance their skills and knowledge.
- Institute of Quality Assurance (IQA): Based in the UK, the IQA is dedicated to promoting quality assurance practices across various industries. It offers professional development opportunities, networking events, and resources for quality professionals.
- Six Sigma Academy: This organization specializes in Six Sigma methodologies, which are widely used in quality control. Membership provides access to training, certification, and a community of professionals dedicated to process improvement.
Benefits of Membership
Joining a professional organization can provide numerous benefits for quality control specialists. Here are some of the key advantages:
- Access to Resources: Members often gain access to exclusive resources, including research papers, case studies, and industry reports. These materials can help professionals stay informed about the latest trends and best practices in quality control.
- Professional Development: Many organizations offer training programs, workshops, and webinars that can enhance a member’s skills and knowledge. These opportunities are invaluable for staying competitive in the field.
- Certification Opportunities: Membership often provides access to certification programs that can enhance a professional’s credentials. Certifications such as Certified Quality Engineer (CQE) or Certified Quality Auditor (CQA) can significantly boost career prospects.
- Networking: Being part of a professional organization allows members to connect with peers, industry leaders, and potential employers. Networking can lead to job opportunities, mentorship, and collaborations on projects.
- Industry Recognition: Membership in a reputable organization can enhance a professional’s credibility and reputation within the industry. It signals a commitment to quality and continuous improvement.
- Access to Conferences and Events: Many organizations host annual conferences, seminars, and workshops that provide opportunities for learning and networking. These events often feature keynote speakers, panel discussions, and breakout sessions on various quality-related topics.
Networking Opportunities
Networking is a vital component of professional growth in any field, and quality control is no exception. Here are some of the key networking opportunities available to quality control specialists:
- Conferences and Workshops: Attending industry conferences and workshops is one of the best ways to meet other professionals in the field. These events often feature sessions on the latest trends, technologies, and methodologies in quality control, providing a platform for discussion and collaboration.
- Local Chapters and Meetups: Many national organizations have local chapters that host regular meetings and events. These gatherings provide an informal setting for quality control professionals to connect, share experiences, and discuss challenges they face in their roles.
- Online Forums and Social Media Groups: In today’s digital age, online platforms have become essential for networking. Many professional organizations have online forums or social media groups where members can ask questions, share insights, and connect with others in the industry. LinkedIn groups focused on quality control can also be valuable for networking.
- Mentorship Programs: Some organizations offer mentorship programs that pair experienced professionals with those new to the field. These relationships can provide guidance, support, and valuable connections that can help advance a quality control specialist’s career.
- Volunteer Opportunities: Getting involved in committees or volunteer opportunities within professional organizations can be an excellent way to meet other members and build relationships. Volunteering can also enhance leadership skills and provide valuable experience.
Professional associations and networking are integral to the success of quality control specialists. By engaging with key organizations, taking advantage of membership benefits, and actively participating in networking opportunities, professionals can enhance their skills, expand their connections, and advance their careers in the ever-evolving field of quality control.
Continuing Education and Professional Development
In the ever-evolving landscape of quality control, the role of a Quality Control Specialist is not static. As industries advance and new technologies emerge, the need for ongoing education and professional development becomes paramount. This section delves into the importance of lifelong learning for Quality Control Specialists, explores available courses and workshops, and discusses how to stay updated with industry trends.
Importance of Lifelong Learning
Lifelong learning is the continuous, voluntary, and self-motivated pursuit of knowledge for personal or professional development. For Quality Control Specialists, this concept is particularly crucial due to several factors:
- Technological Advancements: The quality control field is increasingly influenced by technology, including automation, artificial intelligence, and data analytics. Staying abreast of these advancements ensures that specialists can effectively utilize new tools and methodologies to enhance quality assurance processes.
- Regulatory Changes: Industries such as pharmaceuticals, food production, and manufacturing are subject to stringent regulations that can change frequently. Continuous education helps Quality Control Specialists remain compliant with the latest standards and practices.
- Skill Enhancement: The quality control landscape is broad, encompassing various skills from statistical analysis to problem-solving. Lifelong learning allows specialists to refine existing skills and acquire new ones, making them more versatile and valuable in their roles.
- Career Advancement: Professionals who engage in ongoing education are often better positioned for promotions and leadership roles. Employers value individuals who demonstrate a commitment to personal and professional growth.
Available Courses and Workshops
Quality Control Specialists have access to a variety of educational resources designed to enhance their knowledge and skills. These include formal courses, workshops, and certifications offered by various institutions and organizations. Here are some notable options:
1. Certification Programs
Certifications can significantly bolster a Quality Control Specialist’s credentials. Some of the most recognized certifications include:
- Certified Quality Auditor (CQA): Offered by the American Society for Quality (ASQ), this certification focuses on the principles and practices of auditing quality systems.
- Certified Quality Engineer (CQE): Also provided by ASQ, this certification is aimed at professionals who understand quality engineering principles and practices.
- Six Sigma Certification: Six Sigma methodologies are widely used in quality control. Various organizations offer Six Sigma training, ranging from Yellow Belt to Black Belt levels, focusing on process improvement and quality management.
2. Online Courses
With the rise of online learning platforms, Quality Control Specialists can access a plethora of courses from the comfort of their homes. Some popular platforms include:
- Coursera: Offers courses from universities and institutions on topics such as quality management, statistical process control, and data analysis.
- edX: Provides access to university-level courses, including quality assurance and quality control methodologies.
- Udemy: Features a wide range of courses on specific quality control tools and techniques, often at affordable prices.
3. Workshops and Seminars
In-person workshops and seminars provide hands-on experience and networking opportunities. Many professional organizations, such as ASQ, host events that focus on current trends, best practices, and new technologies in quality control. Attending these events can enhance practical skills and foster connections with industry peers.
Staying Updated with Industry Trends
In addition to formal education, Quality Control Specialists must actively seek out information to stay current with industry trends. Here are several strategies to achieve this:
1. Professional Associations
Joining professional associations, such as the American Society for Quality (ASQ) or the International Organization for Standardization (ISO), can provide access to valuable resources, including publications, webinars, and networking opportunities. These organizations often publish journals and newsletters that highlight the latest research, trends, and best practices in quality control.
2. Industry Conferences
Attending industry conferences is an excellent way to learn about the latest developments in quality control. These events often feature keynote speakers, panel discussions, and workshops led by experts in the field. Conferences also provide a platform for networking with other professionals, sharing experiences, and discussing challenges and solutions.
3. Online Forums and Communities
Participating in online forums and communities, such as LinkedIn groups or specialized quality control forums, allows Quality Control Specialists to engage in discussions, ask questions, and share insights with peers. These platforms can be invaluable for learning about new tools, techniques, and industry challenges.
4. Subscribing to Industry Publications
Staying informed about industry trends can also be achieved by subscribing to relevant publications and journals. Many organizations publish newsletters, magazines, and research papers that cover the latest advancements in quality control. Examples include:
- Quality Progress: A monthly magazine published by ASQ that covers quality management topics, case studies, and best practices.
- Journal of Quality in Maintenance Engineering: Focuses on quality management in maintenance engineering, providing insights into best practices and innovations.
5. Continuous Networking
Building a professional network is essential for staying updated. Engaging with colleagues, mentors, and industry leaders can provide insights into emerging trends and best practices. Networking can occur through formal events, social media platforms, or informal gatherings.
The role of a Quality Control Specialist is dynamic and requires a commitment to lifelong learning and professional development. By engaging in continuous education, pursuing relevant certifications, and staying informed about industry trends, Quality Control Specialists can enhance their skills, remain competitive, and contribute significantly to their organizations’ success.
Key Takeaways
- Understanding the Role: A Quality Control Specialist is essential in ensuring products meet quality standards across various industries, playing a critical role in maintaining customer satisfaction and compliance.
- Core Responsibilities: Key tasks include conducting inspections, testing products, analyzing data, and implementing quality improvement processes to enhance product reliability.
- Essential Skills: Successful specialists possess a mix of technical skills (like proficiency in quality control software) and soft skills (such as attention to detail and effective communication).
- Career Path: Entry-level positions can lead to advanced roles, with opportunities for specialization in areas like regulatory compliance or quality assurance management.
- Salary Insights: Compensation varies based on experience, industry, and location, with additional benefits often enhancing overall remuneration.
- Challenges and Opportunities: While facing challenges such as evolving regulations and technological advancements, there are significant opportunities for growth and professional development in the field.
- Preparation for Success: Aspiring Quality Control Specialists should focus on relevant education, gain practical experience, and prepare thoroughly for interviews to stand out to employers.
- Continuous Learning: Engaging in ongoing education and networking through professional associations is vital for staying current with industry trends and enhancing career prospects.
The role of a Quality Control Specialist is pivotal in ensuring product excellence and compliance. By understanding the responsibilities, required skills, and career pathways, aspiring professionals can effectively navigate their journey in this rewarding field.
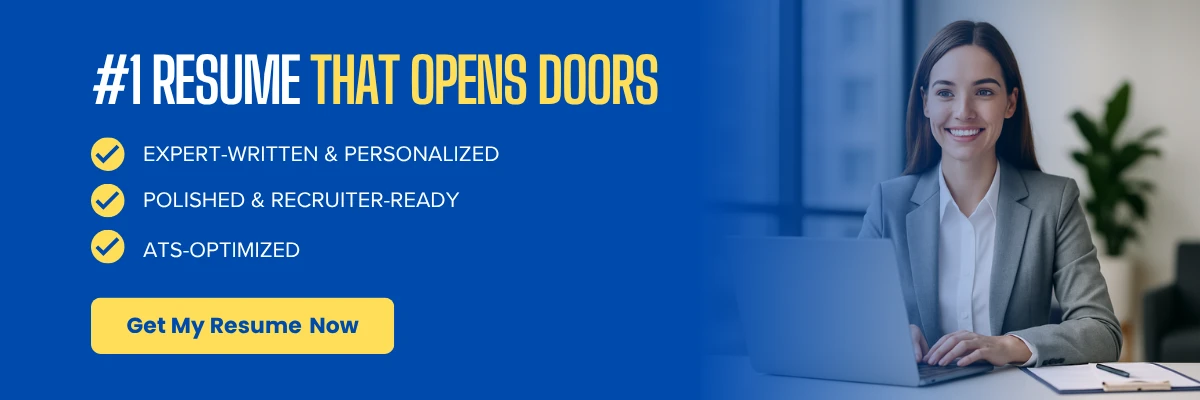
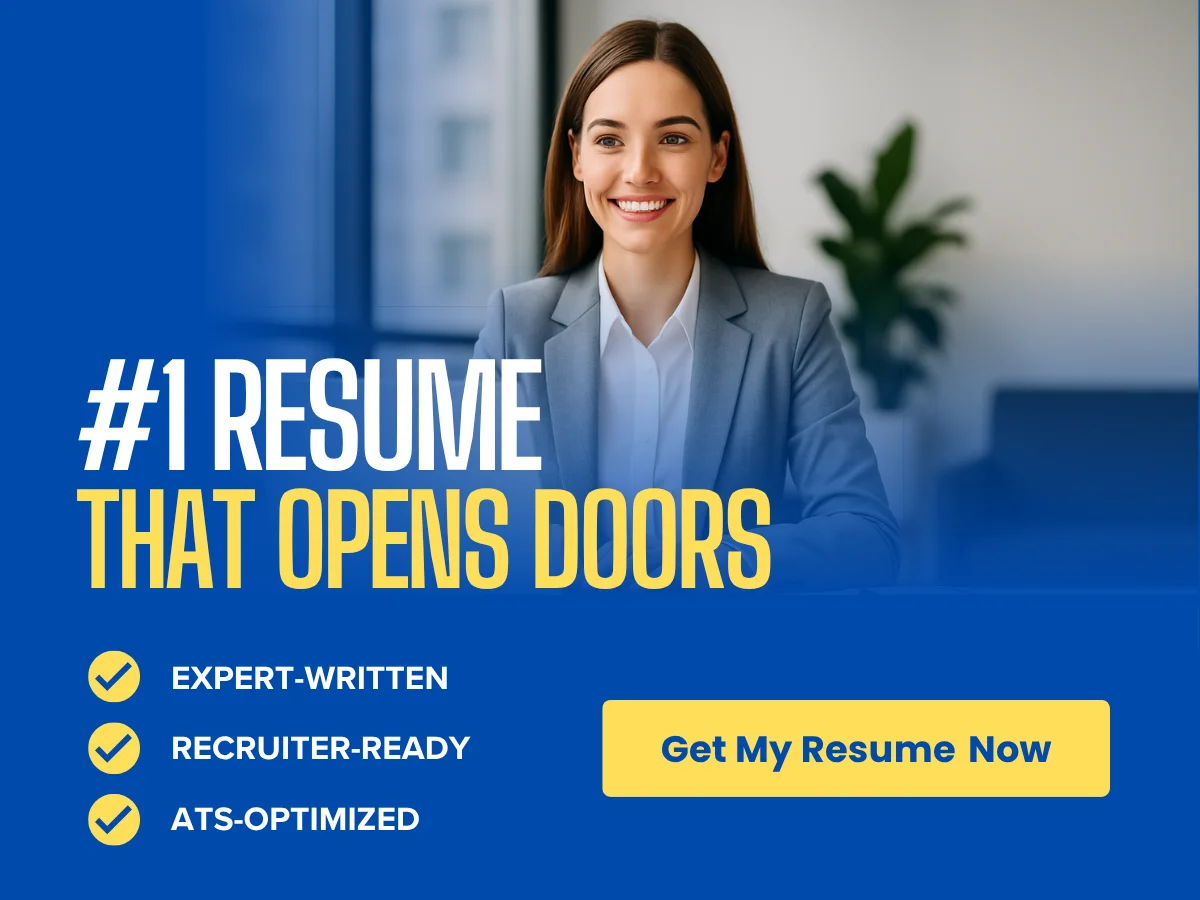